Dixon rings
Dixon rings are a form of random packing used in chemical processing. They consist of a stainless steel mesh formed into a ring with a central divider, and are intended to be packed randomly into a packed column. Dixon rings provide a large surface area and low pressure drop while maintaining a high mass transfer rate, making them useful for distillations and many other applications.
Background
Packed columns
Packed columns are used in a range of industries to allow intimate contact between two immiscible fluids which can be liquid/liquid or liquid/gas. The fluids are passed through in a counter current flow through a column.
Random column packing
Random column packing used to characterize the maximum volume fraction of a solid object obtained when they are packed randomly. This method of packing has been used since the early 1820s; the types of packing used were originally made out of glass spheres. However, in 1850 they were replaced by a more porous pumice stone and pieces of coke.
In the early 20th century Friedrich Raschig realized the importance of a high void fraction and having the internal surface of the packing media take part in the mass transfer. He designed the Raschig ring, which was more effective than previous forms of random packing and became very popular. Raschig rings are usually built from ceramic or metal and provided a large surface area within the column for interaction between liquid and gas vapors.
The development of the Dixon ring
In 1946 Dr Olaf Dixon developed a new product for column distillation. Based on the design of the Lessing ring, Dixon developed the Dixon ring, employing a stainless steel mesh to improve the pressure drop of the packed column.
Application
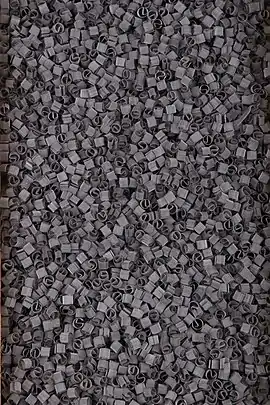
Dixon rings are used for mainly for laboratory distillation applications.
Performance principles
The enhanced performance of the Dixon ring is based on liquid surface tension: when the mesh is wet its surface area increases greatly, with an accompanying increase in the rate of mass transfer. Dixon rings require pre-wetting (flow of liquid over the packed bed prior to starting the reaction flow). While this increases batch processing startup time, the increased performance of the Dixon ring overcomes this.
Property | Ring Size | ||
---|---|---|---|
1/16" | 1/8" | 1/4" | |
Surface area | 3550 | 2378 | 900 |
Void space% | 94.63 | 90.98 | 90.73 |
Number per litre | 102,000 | 24,400 | 2,965 |
See also
References
- Kaba, Akira; Akai, Reijiro; Yamamoto, Ichiro; Kanagawa, Akira (October 1988). "Measurement of HETP of SUS Dixon Ring and Porcelain Packing in Small-Scale Water Distillation Column for H20-HTO Isotope Separation". Nuclear Science and Technology. 25 (10): 69–74.
- Sheng, Miaopeng; Liu, Chenguang; Ge, Chunyuan; Arowo, Moses; Xiang, Yang; Sun, Baochang; Chu, Guangwen; Zou, Haikui (2016). "Mass-Transfer Performance of CO2 Absorption with Aqueous Diethylenetriamine-Based Solutions in a Packed Column with Dixon Rings". Industrial & Engineering Chemistry Research. 55 (40): 10788–10793. doi:10.1021/acs.iecr.6b02280.
- Jin, Yanchao; Hu, Runzhi; Wang, Yiping; Cui, Yong; Liu, Yun; Huang, Qunwu (2017). "The effect of Dixon rings on direct contact heat transfer performance: Comparison of counter and co-current evaporation". Applied Thermal Engineering. 117: 762–772. doi:10.1016/j.applthermaleng.2017.02.054. ISSN 1359-4311.