ELM327
The ELM327 is a programmed microcontroller produced by ELM Electronics for translating the on-board diagnostics (OBD) interface found in most modern cars. The ELM327 command protocol is one of the most popular PC-to-OBD interface standards and is also implemented by other vendors.
The original ELM327 is implemented on the PIC18F2480 microcontroller from Microchip Technology.
ELM327 is one of a family of OBD translators from ELM Electronics. Other variants implement only a subset of the OBD protocols.
Uses
The ELM327 abstracts the low-level protocol and presents a simple interface that can be called via a UART, typically by a hand-held diagnostic tool or a computer program connected by USB, RS-232, Bluetooth or Wi-Fi. New applications include smartphones.
There are a large number of programs available that connect to the ELM327.[1]
The function of such software may include:
- Supplementary vehicle instrumentation
- Reporting of error codes
- Clearing error codes
ELM327 Functions:
- Read diagnostic trouble codes, both generic and manufacturer-specific.
- Clear some trouble codes and turn off the MIL ("Malfunction Indicator Light", more commonly known as the "Check Engine Light")
- Display current sensor data
- Engine RPM
- Calculated Load Value
- Coolant Temperature
- Fuel System Status
- Vehicle Speed
- Short Term Fuel Trim
- Long Term Fuel Trim
- Intake Manifold Pressure
- Timing Advance
- Intake Air Temperature
- Air Flow Rate
- Absolute Throttle Position
- Oxygen sensor voltages/associated short term fuel trims
- Fuel System status
- Fuel Pressure
Protocols supported by ELM327
The protocols supported by ELM327 are:[2]
- SAE J1850 PWM (41.6 kbit/s)
- SAE J1850 VPW (10.4 kbit/s)
- ISO 9141-2 (5 baud init, 10.4 kbit/s)
- ISO 14230-4 KWP (5 baud init, 10.4 kbit/s)
- ISO 14230-4 KWP (fast init, 10.4 kbit/s)
- ISO 15765-4 CAN (11 bit ID, 500 kbit/s)
- ISO 15765-4 CAN (29 bit ID, 500 kbit/s)
- ISO 15765-4 CAN (11 bit ID, 250 kbit/s)
- ISO 15765-4 CAN (29 bit ID, 250 kbit/s)
- SAE J1939 (250kbit/s)
- SAE J1939 (500kbit/s)
ELM327 command set
The ELM327 command set[3][4] is similar to the Hayes AT commands.
Other versions
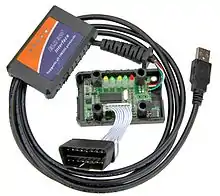
The ELM327 is a PIC microcontroller that has been customized with ELM Electronics' proprietary code that implements the testing protocols. When ELM Electronics sold version 1.0 of its ELM327, it did not enable the copy protection feature of the PIC microcontroller. Consequently, anyone could buy a genuine ELM327, and read ELM's proprietary binary microcontroller software using a device programmer. With this software, pirates could trivially produce ELM327 clones by purchasing the same microcontroller chips and programming them with the copied code.[5][6] ELM327 copies were widely sold in devices claiming to contain an ELM327 device, and problems have been reported with the copies.[7] The problems reflect bugs that were present in ELM's version 1.0 microcode; those making the clones may continue to sell the old version.
Although these copies may contain the ELM327 v1.0 code, they may falsely report the version number as the current version provided by the genuine ELM327, and in some cases report an as-yet non-existent version.[8] Released software versions for the ELM327 are 1.0, 1.0a, 1.1, 1.2, 1.2a, 1.3, 1.3a, 1.4, 1.4b, 2.0, 2.1, 2.2 and 2.3 only.[9] The actual functions of these copies are nonetheless limited to the functions of the original ELM327 v1.0, with their inherent deficiencies.
Version outline
v1.0 Initial public release, the ELM327 v1.0 supported: – SAEJ1850 PWM and VPW,- – ISO 9141-2 (10.4 and 9.6 kbps), – ISO 14230-4 (10.4 and 9.6 kbps), – ISO 15765-4 CAN (250 and 500 kbps)- The RS232 baud rates were only 9.6 kbps or 38.4 kbps
v1.0a – J1850 VPW timing adjustment for some ’99 – ’00 GM trucks.
v1.1 – Introduced Programmable Parameters – Added Flow Control commands
v1.2 – RS232 baud rates are adjustable to 500 kbps – Programmable Parameters can be reset with a jumper – Introduced Adaptive Timing – Added SAE J1939 support (protocol A) – Added user defined CAN protocols B and C – Modified KWP protocols to allow four byte headers
v1.2a – Changed error detection to catch KWP 4 byte headers if no data or checksum – Added check to prevent CAN mask corruption on certain Flow Control sends
v1.3 – Adaptive Timing tuned a little differently – Several J1939 improvements – New CAN CRA commands to help setting masks and filters – New CAN D0/D1 commands for printing of message dlc – New CAN RTR command for sending same – Added space character control in responses – New STOPPED message for user interrupts during searches – Introduced LV RESET message for resets from low voltage – New @2 and @3 commands for storing of unique identifier – Added ability to state the number of responses desired
v1.3a (still available) – Added wiring checks for when the J1962 CAN pins are used for other functions
v1.4 – Added Low Power mode (‘sleep’ function) – Added extended addressing mode for CAN protocols – Added 4800 baud ISO 9141 and ISO 14230 support – Allow manual control over ISO 9141 and ISO 14230 initiation – Provided a single EEPROM byte for user data storage – All interrupts now say STOPPED (not just when searching) – Many new Programmable Parameters and additions
v1.4a Elm Electronics never made a v1.4a
v1.4b (no longer available) – New CSM command to have active or passive CAN monitoring – New CRA command to quickly reset changed masks and filters – Several SAE J1939 updates
v1.5 Elm Electronics never made a v1.5
v2.0 – New Activity Monitor watches OBD pins – Wake from Low Power now retains settings – AT CRAs accept ‘don’t care’s (X’s) – New PP’s provide extensive ISO/KWP control – Increased the RS232 Tx buffer to 512 bytes – Brownout reset voltage reduced to 2.8V
v2.1 – Speed increases – Processes ‘Response Pending’ (7F xx 78) replies – CAN searches now measure frequency and require a match
v2.2 – AT CS command now shows CAN frequency – Added 12500 and 15625 bps ISO/KWP baud rates – New AT CER hh command allows defining the CEA Rx address – New IFR modes 4,5,6 control J1850 IFR sending while monitoring – Added PP 1F to allow KWP length to include the checksum byte – Increased PP19 from 31 to 4F
v2.3 (latest release) – New AT FT command adds another layer of filtering – Added three CAN Flow Control modes for experimenters – Response Pending now works with CAN Extended Addressing – New AT IA, and C0/C1 commands – Better noise tolerance on RS232 Rx
Slightly more detailed changes may be viewed in their latest datasheet in the Version History chapter.[10]
See also
References
- "ELM327 Compatible Software". Retrieved 15 Dec 2020.
- "ELM Electronics". ELM Electronics. ELM Electronics.
- "ELM327 AT Commands" (PDF). ELM Electronics. Retrieved 6 May 2012.
- "ELM327 v2.2 OBD to RS232 Interpreter" (PDF). ELM Electronics. Retrieved 15 Jan 2018.
- "83427-elm327-usb-vehicle-obd-2-scanner-tool". Priuschat forum. Retrieved 6 May 2012.
- "ebay ELM327 mini guide". User review. eBay. Retrieved 6 May 2012.
- "Why you shouldn't buy an Elm327 Clone". Scantool. Retrieved 6 May 2012.
- "ELM327 Product Information". ELM Electronics.
- "ELM327 SW versions". ELM Electronics. Retrieved 28 May 2020.
- "The ELM327 v2.3 data sheet" (PDF). ELM Electronics. Retrieved 28 May 2020.