Ejector venturi scrubber
An ejector or jet venturi scrubber is an industrial pollution control device, usually installed on the exhaust flue gas stacks of large furnaces, but may also be used on any number of other air exhaust systems. This type of technology is a part of the group of air pollution controls collectively referred to as wet scrubbers. Although operating in similar ways to a venturi scrubber the ejector venturi is not driven by the flow of process gas and instead the energy is derived from the high-pressure spray of liquid from a nozzle, allowing the scrubber to also act as a vacuum ejector and draw process gas through the device without external assistance.
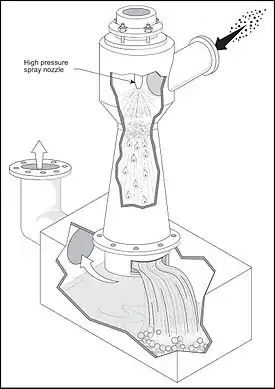
Operation
Like a spray tower an ejector venturi scrubber uses a preformed spray. However, in an ejector venturi scrubber only a single nozzle is used instead of many nozzles. This nozzle operates at higher pressures and higher injection rates than those in most spray chambers. The high-pressure spray nozzle (up to 689 kPa or 100 psig) is aimed at the throat section of a venturi constriction.
The ejector venturi is unique among available scrubbing systems since it can move the process gas without the aid of a fan or blower. The liquid spray coming from the nozzle creates a partial vacuum in the side duct of the scrubber. The partial vacuum is due to the Bernoulli effect, and is similar to water aspirators used in chemistry labs. This partial vacuum can be used to move the process gas through the venturi as well as through the facility's process system. In the case of easily-clogging material, explosive gasses, or extremely corrosive atmospheres, the elimination of a fan in the system can avoid many potential problems.
The energy for the formation of scrubbing droplets comes from the injected liquid. The high pressure sprays passing through the venturi throat form numerous fine liquid droplets that provide turbulent mixing between the gas and liquid phases. Very high liquid-injection rates are used to provide the gas-moving capability and higher collection efficiencies. As with other types of venturis, a means of separating entrained liquid from the gas stream must be installed. Entrainment separators are commonly used to remove remaining small droplets.
Particle collection
Ejector venturis are effective in removing particles larger than 1.0 μm in diameter. These scrubbers are not used on submicrometer-sized particles unless the particles are condensable [Gilbert, 1977]. Particle collection occurs primarily by impaction as the exhaust gas (from the process) passes through the spray.
The turbulence that occurs in the throat area also causes the particles to contact the wet droplets and be collected. Particle collection efficiency increases with an increase in nozzle pressure and/or an increase in the liquid-to-gas ratio. Increases in either of these two operating parameters will also result in an increase in pressure drop for a given system. Therefore, an increase in pressure drop also increases particle collection efficiency. Ejector venturis operate at higher L/G ratios than most other particulate scrubbers (i.e., 7 to 13 l/m3 compared to 0.4-2.7 l/m3 for most other designs), and often also require higher liquid pressures, especially if being used to drive the process gas.
Gas collection
Ejector venturis have a short gas-liquid contact time because the exhaust gas velocities through the vessel are very high. This short contact time limits the absorption efficiency of the system. Although ejector venturis are not used primarily for gas removal, they can be effective if the gas is very soluble or if a very reactive scrubbing reagent is used. In these instances, removal efficiencies of as high as 95% can be achieved [Gilbert, 1977].
Maintenance problems
Ejector venturis are subject to abrasion problems in the high-velocity areas - nozzle and throat. Both must be constructed of wear-resistant materials because of the high liquid injection rates and nozzle pressures. Maintaining the pump that recirculates liquid is also very important. In addition, the high gas velocities necessitate the use of entrainment separators to prevent excessive liquid carryover. The separators should be easily accessible or removable so that they can be cleaned if plugging occurs.
Summary
Because of their open design and the fact that they do not require a fan, ejector venturis are capable of handling a wide range of corrosive and/or sticky particles. However, they are not very effective in removing submicrometer particles. They have an advantage in being able to handle small, medium and large exhaust flows. They can be used singly or in multiple stages of two or more in series, depending on the specific application.
Multiple-stage systems have been used where extremely high collection efficiency of particles or gaseous pollutants was necessary. Multiple-stage systems provide increased gas-liquid contact time, thus increasing absorption efficiency.
Table 1 lists the operating parameters for ejector venturis.[1]
Table 1. Operating characteristics of ejector venturis | |||||
---|---|---|---|---|---|
Pollutant | Pressure drop (Δp) | Liquid-to-gas ratio (L/G) | Liquid-inlet pressure (pL) | Removal efficiency | Applications |
Gases | 1.3–13 cm of water | 7-13 l/m3 | 100-830 kPa | 95% for very soluble gases | Pulp and paper industry Chemical process industry Food industry Metals processing industry |
Particles | 0.5-5 in of water | 50-100 gal/1,000 ft3 | 15-120 psig | 1 μm diameter |
Bibliography
- Bethea, R. M. 1978. Air Pollution Control Technology. New York: Van Nostrand Reinhold.
- Gilbert, J. W. 1977. Jet venturi fume scrubbing. In P. N. Cheremisinoff and R. A. Young (Eds.), Air Pollution Control and Design Handbook. Part 2. New York: Marcel Dekker.
- McIlvaine Company. 1974. The Wet Scrubber Handbook. Northbrook, IL: McIlvaine Company.
- Richards, J. R. 1995. Control of Particulate Emissions (APTI Course 413). U.S. Environmental Protection Agency.
- Richards, J. R. 1995. Control of Gaseous Emissions. (APTI Course 415). U.S. Environmental Protection Agency.
References
![]() |
Wikimedia Commons has media related to Venturi scrubbers. |
-
- US EPA Air Pollution Training Institute developed in collaboration with North Carolina State University, College of Engineering (NCSU)