Stabilizer (ship)
Ship stabilizers (or stabilisers) are fins or rotors mounted beneath the waterline and emerging laterally from the hull to reduce a ship's roll due to wind or waves. Active fins are controlled by a gyroscopic control system. When the gyroscope senses the ship roll, it changes the fins' angle of attack to exert force to counteract the roll. Fixed fins and bilge keels do not move; they reduce roll by hydrodynamic drag exerted when the ship rolls. Stabilizers are mostly used on ocean-going ships.
.PNG.webp)
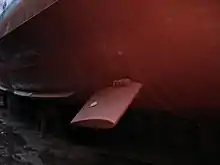
Function
Fins work by producing lift or downforce when the vessel is in motion. The lift produced by the fins should work against the roll moment of the vessel. To accomplish this, two wings, each installed underwater on either side of the ship, are used. Stabilizers can be:
- Retractable - All medium and large cruise and ferry ships have the ability to retract the fins into a space inside the hull in order to avoid extra fuel consumption and reduce the required hull clearance when the fins are not needed
- Non-retractable - Used on small vessels such as yachts.
Stabilizer movement is similar to that of aircraft ailerons. Some types of fins, especially the ones installed on larger ships, are provided with flaps, that increase the fin lift by about 15%. Stabilizer control needs to consider numerous variables that change quickly: wind, waves, ship motion, draft, etc. Fin stabilizers are much more efficient at higher velocities and lose effectiveness when the ship is under a minimum speed.[1] Stabilization solutions at anchor or at low speed include actively controlled fins (such as the stabilisation at rest system developed by Rolls Royce[2] that oscillate to counteract wave motion), and rotary cylinders employing the Magnus effect. The latter two systems are retractable, allowing for a thinner vessel profile when docking and reducing drag while cruising.
History

One early stabilization technology is the anti-rolling gyro, or gyroscopic stabilization. The World War I transport USS Henderson, completed in 1917, was the first large ship with gyro stabilizers. It had two 25-ton, 9-foot diameter flywheels mounted near the center of the ship, spun at 1100 RPM by 75 HP AC motors. The gyroscopes' cases were mounted on vertical bearings. When a small sensor gyroscope on the bridge sensed a roll, a servomotor would rotate the gyros about a vertical axis in a direction so their precession would counteract the roll. In tests this system was able to reduce roll to 3 degrees in the roughest seas. One of the most famous ships to first use an anti-rolling gyro was the Italian passenger liner SS Conte di Savoia, which first sailed in November 1932. It had three flywheels which were 13 feet in diameter and weighed 108 tons.[3] Gyroscope stabilization was replaced by fin stabilization due to its lower weight and bulk, but it has seen renewed interest since the 1990s (Seakeeper, etc.).
The passive bilge keel is an early 20th-century stabilizing innovation, not as effective at reducing roll, but easier to install, and does not require space inside the hull.
The first mention of automatic fin stabilizers for ships was in 1932 by an engineer working for General Electric.[4]
The first use of fin stabilizers on a ship was by a Japanese cruise liner in 1933.[5]
In 1934 a Dutch liner introduced one of the world's most unusual ship stabilizer systems, in which two large tubes were mounted on each side of the ship's hull with the bottom of the tubes open to the sea. The top of the tubes had compressed air or steam pumped in. As the ship rolled, the side it was rolling to would fill with water and then compressed air or steam would be injected to push the water down, countering the roll.[6]
In 2018, rocket and space technology company Blue Origin purchased the Stena Freighter, a roll-on/roll-off cargo ship, for use as a landing platform ship for its New Glenn launch vehicle booster stages. As of late 2018, the ship is undergoing refit to prepare for its role of landing rockets.[7] The rocket boosters will be recovered downrange of the launch site in the Atlantic Ocean while the hydrodynamically-stabilized ship is underway. The ship stabilization technology is designed to increase the likelihood of successful rocket recovery in rough seas, as well as helping to carry out launches on schedule.[8][9]
![]() |
Wikimedia Commons has media related to Ship stabilizers. |
References
- "Quantum Rotary Stabilizers" (video). YouTube. 2 June 2009.
- "Stabilisation at rest". Products. Rolls-Royce Group PLC.
- "Italian Liner To Defy The Waves" Popular Mechanics, April 1931.
- "Fins Proposed For Big Liners To Prevent Rolling". Popular Mechanics. August 1932. p. 251.
- "Fins to Stop Ship's Rolling Governed by Gyro". Popular Mechanics. April 1933. p. 509.
- "Compressed Air Stabilizer Stops Roll of Ship". Popular Mechanics. October 1934. p. 573.
- Tribou, Richard (24 October 2018). "Cargo ship for Blue Origin's New Glenn launches arrives to Florida". Orlando Sentinel. Retrieved 25 November 2018.
- Burghardt, Thomas (20 September 2018). "Building on New Shepard, Blue Origin to pump a billion dollars into New Glenn readiness". NASASpaceFlight.com. Retrieved 22 September 2018.
- Burns, Matt (7 March 2017). "Blue Origin reveals the 'New Glenn' takeoff and landing sequence in new video". TechCrunch. Retrieved 26 November 2018.