Bioplastic
Bioplastics are plastic materials produced from renewable biomass sources, such as vegetable fats and oils, corn starch, straw, woodchips, sawdust, recycled food waste, etc. Bioplastic can be made from agricultural by-products and also from used plastics (i.e. plastic bottles and other containers) by using microorganisms. Bioplastics are usually derived from sugar derivatives, including starch, cellulose, and lactic acid. Common plastics, such as fossil-fuel plastics (also called petrobased polymers) are derived from petroleum or natural gas.
As of 2014, bioplastics represented approximately 0.2% of the global polymer market (300 million tons).[1]Although bioplastics are not commercially significant, research continues on this topic.[2]
from the biomass and which, at some stage in its processing into finished
products, can be shaped by flow.
Note 1: | Bioplastic is generally used as the opposite of polymer derived from fossil resources. |
Note 2: | Bioplastic is misleading because it suggests that any polymer derived from the biomass is environmentally friendly. |
Note 3: | The use of the term "bioplastic" is discouraged. Use the expression "biobased polymer". |
Note 4: | A biobased polymer similar to a petrobased one does not imply any superiority with respect to the environment unless the comparison of respective life cycle assessments is favourable.[3] |



In addition to being decoupled from the petrochemical industry, bioplastics are attractive because they are biodegradable. Not all bioplastics are biodegradable nor biodegrade more readily than commodity fossil-fuel derived plastics.[4][3]
Proposed applications
Bioplastics are used for disposable items, such as packaging, crockery, cutlery, pots, bowls, and straws.[5] Few commercial applications exist for bioplastics. Cost and performance remain problematic. Typical is the example of Italy, where biodegradable plastic bags and shoppers are compulsory since 2011 with the introduction of a specific law.[6] Beyond structural materials, electroactive bioplastics are being developed that promise to carry electric current.[7]
Biopolymers are available as coatings for paper rather than the more common petrochemical coatings.[8]
Bioplastics called drop-in bioplastics are chemically identical to their fossil-fuel counterpart but made from renewable resources. Examples include bio-PE, bio-PET, bio-propylene, bio-PP,[9] and biobased nylons.[10][11][12] Drop-in bioplastics are easy to implement technically, as existing infrastructure can be used.[13] A dedicated bio-based pathway allows to produce products that can not be obtained through traditional chemical reactions and can create products which have unique and superior properties, compared to fossil-based alternatives.[14]
Types
Starch-based plastics
Thermoplastic starch represents the most widely used bioplastic, constituting about 50 percent of the bioplastics market.[15] Simple starch bioplastic film can be made at home by gelatinizing starch and solution casting.[16] Pure starch is able to absorb humidity, and is thus a suitable material for the production of drug capsules by the pharmaceutical sector. However, pure starch-based bioplastic is brittle. Plasticizer such as glycerol, glycol, and sorbitol and can also be added so that the starch can also be processed thermo-plastically.[17] The characteristics of the resulting bioplastic (also called "thermoplastic starch") can be tailored to specific needs by adjusting the amounts of these additives. Conventional polymer processing techniques can be used to process starch into bioplastic, such as extrusion, injection molding, compression molding and solution casting.[17] The properties of starch bioplastic is largely influenced by amylose/amylopectin ratio. Generally, high-amylose starch results in superior mechanical properties.[18] However, high-amylose starch has less processiblity because of its higher gelatinization temperature[19] and higher melt viscosity.[20]
Starch-based bioplastics are often blended with biodegradable polyesters to produce starch/polylactic acid,[21] starch/polycaprolactone[22] or starch/Ecoflex[23] (polybutylene adipate-co-terephthalate produced by BASF[24]) blends. These blends are used for industrial applications and are also compostable. Other producers, such as Roquette, have developed other starch/polyolefin blends. These blends are not biodegradable, but have a lower carbon footprint than petroleum-based plastics used for the same applications.[25]
Starch is cheap, abundant, and renewable.[26]
Starch-based films (mostly used for packaging purposes) are made mainly from starch blended with thermoplastic polyesters to form biodegradable and compostable products. These films are seen specifically in consumer goods packaging of magazine wrappings and bubble films. In food packaging, these films are seen as bakery or fruit and vegetable bags. Composting bags with this films are used in selective collecting of organic waste.[26] Further, starch-based films can be used as a paper.[27][28]
Starch-based nanocomposites have been widely studied, showing improved mechanical properties, thermal stability, moisture resistance, and gas barrier properties.[29]
Cellulose-based plastics

Cellulose bioplastics are mainly the cellulose esters, (including cellulose acetate and nitrocellulose) and their derivatives, including celluloid.
Cellulose can become thermoplastic when extensively modified. An example of this is cellulose acetate, which is expensive and therefore rarely used for packaging. However, cellulosic fibers added to starches can improve mechanical properties, permeability to gas, and water resistance due to being less hydrophilic than starch.[26]
A group at Shanghai University was able to construct a novel green plastic based on cellulose through a method called hot pressing.[30]
Protein-based plastics
Bioplastics can be made from proteins from different sources. For example, wheat gluten and casein show promising properties as a raw material for different biodegradable polymers.[31]
Additionally, soy protein is being considered as another source of bioplastic. Soy proteins have been used in plastic production for over one hundred years. For example, body panels of an original Ford automobile were made of soy-based plastic.[32]
There are difficulties with using soy protein-based plastics due to their water sensitivity and relatively high cost. Therefore, producing blends of soy protein with some already-available biodegradable polyesters improves the water sensitivity and cost.[33]
Some aliphatic polyesters
The aliphatic biopolyesters are mainly polyhydroxyalkanoates (PHAs) like the poly-3-hydroxybutyrate (PHB), polyhydroxyvalerate (PHV) and polyhydroxyhexanoate (PHH).
Polylactic acid (PLA)

Polylactic acid (PLA) is a transparent plastic produced from maize[34] or dextrose. Superficially, it is similar to conventional petrochemical-based mass plastics like PS. It has the distinct advantage of degrading to nontoxic products. Unfortunately it exhibits inferior impact strength, thermal robustness, and barrier properties (blocking air transport across the membrane).[1] PLA and PLA blends generally come in the form of granulates with various properties, and are used in the plastic processing industry for the production of films, fibers, plastic containers, cups and bottles. PLA is also the most common type of plastic filament used for home fused deposition modeling.
Poly-3-hydroxybutyrate
The biopolymer poly-3-hydroxybutyrate (PHB) is a polyester produced by certain bacteria processing glucose, corn starch[35] or wastewater.[36] Its characteristics are similar to those of the petroplastic polypropylene. PHB production is increasing. The South American sugar industry, for example, has decided to expand PHB production to an industrial scale. PHB is distinguished primarily by its physical characteristics. It can be processed into a transparent film with a melting point higher than 130 degrees Celsius, and is biodegradable without residue.
Polyhydroxyalkanoates
Polyhydroxyalkanoates are linear polyesters produced in nature by bacterial fermentation of sugar or lipids. They are produced by the bacteria to store carbon and energy. In industrial production, the polyester is extracted and purified from the bacteria by optimizing the conditions for the fermentation of sugar. More than 150 different monomers can be combined within this family to give materials with extremely different properties. PHA is more ductile and less elastic than other plastics, and it is also biodegradable. These plastics are being widely used in the medical industry.
Polyamide 11
PA 11 is a biopolymer derived from natural oil. It is also known under the tradename Rilsan B, commercialized by Arkema. PA 11 belongs to the technical polymers family and is not biodegradable. Its properties are similar to those of PA 12, although emissions of greenhouse gases and consumption of nonrenewable resources are reduced during its production. Its thermal resistance is also superior to that of PA 12. It is used in high-performance applications like automotive fuel lines, pneumatic airbrake tubing, electrical cable antitermite sheathing, flexible oil and gas pipes, control fluid umbilicals, sports shoes, electronic device components, and catheters.
A similar plastic is Polyamide 410 (PA 410), derived 70% from castor oil, under the trade name EcoPaXX, commercialized by DSM.[37] PA 410 is a high-performance polyamide that combines the benefits of a high melting point (approx. 250 °C), low moisture absorption and excellent resistance to various chemical substances.
Bio-derived polyethylene
The basic building block (monomer) of polyethylene is ethylene. Ethylene is chemically similar to, and can be derived from ethanol, which can be produced by fermentation of agricultural feedstocks such as sugar cane or corn. Bio-derived polyethylene is chemically and physically identical to traditional polyethylene – it does not biodegrade but can be recycled. The Brazilian chemicals group Braskem claims that using its method of producing polyethylene from sugar cane ethanol captures (removes from the environment) 2.15 tonnes of CO
2 per tonne of Green Polyethylene produced.
Genetically modified feedstocks
With GM corn being a common feedstock, it is unsurprising that some bioplastics are made from this.
Under the bioplastics manufacturing technologies there is the "plant factory" model, which uses genetically modified crops or genetically modified bacteria to optimise efficiency.
Polyhydroxyurethanes
The condensation of polyamines and cyclic carbonates produces polyhydroxurethanes.[38] Unlike traditional cross-linked polyurethanes, cross-linked polyhydroxyurethanes are in principle amenable to recycling and reprocessing through dynamic transcarbamoylation reactions.[39]
Lipid derived polymers
A number bioplastic classes have been synthesized from plant and animal derived fats and oils.[40] Polyurethanes,[41][42] polyesters,[43] epoxy resins[44] and a number of other types of polymers have been developed with comparable properties to crude oil based materials. The recent development of olefin metathesis has opened a wide variety of feedstocks to economical conversion into biomonomers and polymers.[45] With the growing production of traditional vegetable oils as well as low cost microalgae derived oils,[46] there is huge potential for growth in this area.
Environmental impact




Materials such as starch, cellulose, wood, sugar and biomass are used as a substitute for fossil fuel resources to produce bioplastics; this makes the production of bioplastics a more sustainable activity compared to conventional plastic production.[47] The environmental impact of bioplastics is often debated, as there are many different metrics for "greenness" (e.g., water use, energy use, deforestation, biodegradation, etc.).[48][49][50] Hence bioplastic environmental impacts are categorized into nonrenewable energy use, climate change, eutrophication and acidification.[51] Bioplastic production significantly reduces greenhouse gas emissions and decreases non-renewable energy consumption.[47] Firms worldwide would also be able to increase the environmental sustainability of their products by using bioplastics [52]
Although bioplastics save more nonrenewable energy than conventional plastics and emit less GHG compared to conventional plastics, bioplastics also have negative environmental impacts such as eutrophication and acidification.[51] Bioplastics induce higher eutrophication potentials than conventional plastics.[51] Biomass production during industrial farming practices causes nitrate and phosphate to filtrate into water bodies; this causes eutrophication, the process in which a body of water richness gains excessive richness of nutrients.[51] Eutrophication is a threat to water resources around the world since it causes harmful algal blooms that create oxygen dead zones, killing aquatic animals.[53] Bioplastics also increase acidification.[51] The high increase in eutrophication and acidification caused by bioplastics is also caused by using chemical fertilizer in the cultivation of renewable raw materials to produce bioplastics.[47]
Other environmental impacts of bioplastics include exerting lower human and terrestrial ecotoxicity and carcinogenic potentials compared to conventional plastics.[51] However, bioplastics exert higher aquatic ecotoxicity than conventional materials.[51] Bioplastics and other bio-based materials increase stratospheric ozone depletion compared to conventional plastics; this is a result of nitrous oxide emissions during fertilizer application during industrial farming for biomass production.[51] Artificial fertilizer increase nitrous oxide emissions especially when the crop does not need all the nitrogen.[54] Minor environmental impacts of bioplastics include toxicity through using pesticides on the crops used to make bioplastics.[47] Bioplastics also cause carbon dioxide emissions from harvesting vehicles.[47] Other minor environmental impacts include high water consumption for biomass cultivation, soil erosion, soil carbon losses and loss of biodiversity, and they are mainly are a result of land use associated with bioplastics.[51] Land use for bioplastics production leads to lost carbon sequestration and increases the carbon costs while diverting land from its existing uses [55]
Although bioplastics are extremely advantageous because they reduce non-renewable consumption and GHG emissions, they also negatively affect the environment through land and water consumption, using pesticide and fertilizer, eutrophication and acidification; hence one's preference for either bioplastics or conventional plastics depends on what one considers the most important environmental impact.[47]
Another issue with bioplastics, is that some bioplastics are made from the edible parts of crops. This makes the bioplastics compete with food production because the crops that produce bioplastics can also be used to feed people.[56] These bioplastics are called "1st generation feedstock bioplastics". 2nd generation feedstock bioplastics use non-food crops (cellulosic feedstock) or waste materials from 1st generation feedstock (e.g. waste vegetable oil). 3rd generation feedstock bioplastics use algae as the feedstock.[57]
Biodegradation of Bioplastics

Biodegradation of any plastic is a process that happens at solid/liquid interface whereby the enzymes in the liquid phase depolymerize the solid phase [58] Certain types of bioplastics as well as conventional plastics containing additives are able to biodegrade.[59] Bioplastics are able to biodegrade in different environments hence they are more acceptable than conventional plastics.[60] Biodegradability of bioplastics occurs under various environmental conditions including soil, aquatic environments and compost.[60] Both the structure and composition of biopolymer or bio-composite have an effect on the biodegradation process, hence changing the composition and structure might increase biodegradability.[60] Soil and compost as environment conditions are more efficient in biodegradation due to their high microbial diversity.[60] Composting not only biodegrades bioplastics efficiently but it also significantly reduces the emission of greenhouse gases.[60] Biodegradability of bioplastics in compost environments can be upgraded by adding more soluble sugar and increasing temperature.[60] Soil environments on the other hand have high diversity of microorganisms making it easier for biodegradation of bioplastics to occur.[60] However, bioplastics in soil environments need higher temperatures and a longer time to biodegrade.[60] Some bioplastics biodegrade more efficiently in water bodies and marine systems; however, this causes danger to marine ecosystems and freshwater.[60] Hence it is accurate to conclude that biodegradation of bioplastics in water bodies which leads to the death of aquatic organisms and unhealthy water can be noted as one of the negative environmental impacts of bioplastics.
Industry and markets

While plastics based on organic materials were manufactured by chemical companies throughout the 20th century, the first company solely focused on bioplastics- Marlborough Biopolymers- was founded in 1983. However, Marlborough and other ventures that followed failed to find commercial success, with the first such company to secure long-term financial success being the Italian company Novamont, founded in 1989.[61]
Bioplastics remain less than one percent of all plastics manufactured worldwide,[62][63] Most bioplastics do not yet save more carbon emissions than are required to manufacture them.[64] It is estimated that replacing 250 million tons of the plastic manufactured each year with bio-based plastics would require 100 million hectares of land, or 7 percent of the arable land on Earth. And when bioplastics reach the end of their life cycle, those designed to be compostable and marketed as biodegradable are often sent to landfills due to the lack of proper composting facilities or waste sorting, where they then release methane as they break down anaerobically.[65]
COPA (Committee of Agricultural Organisation in the European Union) and COGEGA (General Committee for the Agricultural Cooperation in the European Union) have made an assessment of the potential of bioplastics in different sectors of the European economy:
Sector | Tonnes per year | |
---|---|---|
Catering products | 450,000 | |
Organic waste bags | 100,000 | |
Biodegradable mulch foils | 130,000 | |
Biodegradable foils for diapers | 80,000 | |
Diapers, 100% biodegradable | 240,000 | |
Foil packaging | 400,000 | |
Vegetable packaging | 400,000 | |
Tyre components | 200,000 | |
Total: | 2,000,000 |
History and development of bioplastics
- 1862: At the Great London Exhibition, Alexander Parkes displays Parkesine, the first plastic. Parkesine is made from nitrocellulose. (White 1998)[66]
- 1897: Still produced today, Galalith is a milk-based bioplastic that was created by German chemists in 1897. Galalith is primarily found in buttons. (Thielen 2014) [67]
- 1907: Leo Baekeland invented Bakelite, which received the National Historic Chemical Landmark for its non-conductivity and heat-resistant properties. It is used in radio and telephone casings, kitchenware, firearms and many more products. (Pathak, Sneha, Mathew 2014)
- 1912: Brandenberger invents Cellophane out of wood, cotton, or hemp cellulose. (Thielen 2014) [67]
- 1920s: Wallace Carothers finds Polylactic Acid (PLA) plastic. PLA is incredibly expensive to produce and is not mass-produced until 1989. (Whiteclouds 2018)
- 1926: Maurice Lemoigne invents polyhydroxybutyrate (PHB) which is the first bioplastic made from bacteria. (Thielen 2014) [67]
- 1930s: The first bioplastic car was made from soy beans by Henry Ford. (Thielen 2014) [67][68]
- 1940-1945: During World War II, an increase in plastic production is seen as it is used in many wartime materials. Due to government funding and oversight the United States production of plastics (in general, not just bioplastics) tripled during 1940-1945(Rogers 2005).[69] The 1942 U.S. government short film The Tree in a Test Tube illustrates the major role bioplastics played in the World War II victory effort and the American economy of the time.
- 1950s: Amylomaize (>50% amylose content corn) was successfully bred and commercial bioplastics applications started to be explored. (Liu, Moult, Long, 2009)[70] A decline in bioplastic development is seen due to the cheap oil prices, however the development of synthetic plastics continues.
- 1970s: The environmental movement spurred more development in bioplastics. (Rogers 2005) [69]
- 1983: The first bioplastics company, Marlborough Biopolymers, is started which uses a bacteria-based bioplastic called biopal. (Feder 1985) [71]
- 1989: The further development of PLA is made by Dr. Patrick R. Gruber when he figures out how to create PLA from corn. (Whiteclouds 2018). The leading bioplastic company is created called Novamount. Novamount uses matter-bi, a bioplastic, in multiple different applications. (Novamount 2018) [72]
- 1992: It is reported in Science that PHB can be produced by the plant Arabidopsis thaliana. (Poirier, Dennis, Klomparens, Nawrath, Somerville 1992) [73]
- Late 1990s: The development of TP starch and BIOPLAST from research and production of the company BIOTEC lead to the BIOFLEX film. BIOFLEX film can be classified as blown film extrusion, flat film extrusion, and injection moulding lines. These three classifications have applications as follows: Blown films - sacks, bags, trash bags, mulch foils, hygiene products, diaper films, air bubble films, protective clothing, gloves, double rib bags, labels, barrier ribbons; Flat films - trays, flower pots, freezer products and packaging, cups, pharmaceutical packaging; Injection moulding - disposable cutlery, cans, containers, performed pieces, CD trays, cemetery articles, golf tees, toys, writing materials. (Lorcks 1998) [74]
- 2001: Metabolix inc. purchases Monsanto's biopol business (originally Zeneca) which uses plants to produce bioplastics. (Barber and Fisher 2001) [75]
- 2001: Nick Tucker uses elephant grass as a bioplastic base to make plastic car parts. (Tucker 2001) [76]
- 2005: Cargill and Dow Chemicals is rebranded as NatureWorks and becomes the leading PLA producer. (Pennisi 2016) [77]
- 2007: Metabolix inc. market tests its first 100% biodegradable plastic called Mirel, made from corn sugar fermentation and genetically engineered bacteria. (Digregorio 2009) [78]
- 2012: A bioplastic is developed from seaweed proving to be one of the most environmentally friendly bioplastics based on research published in the journal of pharmacy research. (Rajendran, Puppala, Sneha, Angeeleena, Rajam 2012) [79]
- 2013: a patent is put on bioplastic derived from blood and a crosslinking agent like sugars, proteins, etc. (iridoid derivatives, diimidates, diones, carbodiimides, acrylamides, dimethylsuberimidates, aldehydes, Factor XIII, dihomo bifunctional NHS esters, carbonyldiimide, glyoxyls, proanthocyanidin, reuterin). This invention can be applied by using the bioplastic as tissue, cartilage, tendons, ligaments, bones, and being used in stem cell delivery. (Campbell, Burgess, Weiss, Smith 2013) [80]
- 2014: It is found in a study published in 2014 that bioplastics can be made from blending vegetable waste (parsley and spinach stems, the husks from cocoa, the hulls of rice, etc.) with TFA solutions of pure cellulose creates a bioplastic. (Bayer, Guzman-Puyol, Heredia-Guerrero, Ceseracciu, Pignatelli, Ruffilli, Cingolani, and Athanassiou 2014) [81]
- 2016: An experiment finds that a car bumper that passes regulation can be made from nano-cellulose based bioplastic biomaterials using banana peels. (Hossain, Ibrahim, Aleissa 2016) [82]
- 2017: A new proposal for bioplastics made from Lignocellulosics resources (dry plant matter). (Brodin, Malin, Vallejos, Opedal, Area, Chinga-Carrasco 2017) [83]
- 2018: Many developments occur including Ikea starting industrial production of bioplastics furniture (Barret 2018), Project Effective focusing on replacing nylon with bio-nylon (Barret 2018), and the first packaging made from fruit (Barret 2018).[84]
- 2019: Five different types of Chitin nanomaterials were extracted and synthesized by the 'Korea Research Institute of Chemical Technology' to verify strong personality and antibacterial effects. When buried underground, 100% biodegradation was possible within 6 months.[85]
*This is not a comprehensive list. These inventions were by the author to show versatility of bioplastics and important breakthroughs. New applications and inventions of bioplastics happen every year.
Year | Bioplastic Discovery or Development |
---|---|
1862 | Parkesine - Alexander Parkes |
1868 | Celluloid - John Wesley Hyatt |
1897 | Galalith - German chemists |
1907 | Bakelite - Leo Baekeland |
1912 | Cellophane - Jacques E. Brandenberger |
1920s | Polylactic ACid (PLA) - Wallace Carothers |
1926 | Polyhydroxybutyrate (PHB) - Maurice Lemoigne |
1930s | Soy bean-based bioplastic car - Henry Ford |
1983 | Biopal - Marlborough Biopolymers |
1989 | PLA from corn - Dr. Patrick R. Gruber; Matter-bi - Novamount |
1992 | PHB can be produced by Arabidopsis thaliana (a small flowering plant) |
1998 | Bioflex film (blown, flat, injection molding) leads to many different applications of bioplastic |
2001 | PHB can be produced by elephant grass |
2007 | Mirel (100% biodegradable plastic) by Metabolic inc. is market tested |
2012 | Bioplastic is developed from seaweed |
2013 | Bioplastic made from blood and a cross-linking agent which is used in medical procedures |
2014 | Bioplastic made from vegetable waste |
2016 | Car bumper made from banana peel bioplastic |
2017 | Bioplastics made from lignocellulosic resources (dry plant matter) |
2018 | Bioplastic furniture, bio-nylon, packaging from fruit |
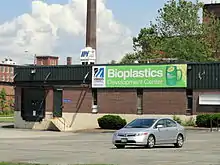

Testing procedures

Industrial compostability – EN 13432, ASTM D6400
The EN 13432 industrial standard must be met in order to claim that a plastic product is compostable in the European marketplace. In summary, it requires multiple tests and sets pass/fail criteria, including disintegration (physical and visual break down) of the finished item within 12 weeks, biodegradation (conversion of organic carbon into CO2) of polymeric ingredients within 180 days, plant toxicity and heavy metals. The ASTM 6400 standard is the regulatory framework for the United States and as similar requirements.
Many starch-based plastics, PLA-based plastics and certain aliphatic-aromatic co-polyester compounds, such as succinates and adipates, have obtained these certificates. Additive-based bioplastics sold as photodegradable or Oxo Biodegradable do not comply with these standards in their current form.
Compostability – ASTM D6002
The ASTM D 6002 method for determining the compostability of a plastic defined the word compostable as follows:
that which is capable of undergoing biological decomposition in a compost site such that the material is not visually distinguishable and breaks down into carbon dioxide, water, inorganic compounds and biomass at a rate consistent with known compostable materials.[86]
This definition drew much criticism because, contrary to the way the word is traditionally defined, it completely divorces the process of "composting" from the necessity of it leading to humus/compost as the end product. The only criterion this standard does describe is that a compostable plastic must look to be going away as fast as something else one has already established to be compostable under the traditional definition.
Withdrawal of ASTM D 6002
In January 2011, the ASTM withdrew standard ASTM D 6002, which had provided plastic manufacturers with the legal credibility to label a plastic as compostable. Its description is as follows:
This guide covered suggested criteria, procedures, and a general approach to establish the compostability of environmentally degradable plastics.[87]
The ASTM has yet to replace this standard.
Biobased – ASTM D6866
The ASTM D6866 method has been developed to certify the biologically derived content of bioplastics. Cosmic rays colliding with the atmosphere mean that some of the carbon is the radioactive isotope carbon-14. CO2 from the atmosphere is used by plants in photosynthesis, so new plant material will contain both carbon-14 and carbon-12. Under the right conditions, and over geological timescales, the remains of living organisms can be transformed into fossil fuels. After ~100,000 years all the carbon-14 present in the original organic material will have undergone radioactive decay leaving only carbon-12. A product made from biomass will have a relatively high level of carbon-14, while a product made from petrochemicals will have no carbon-14. The percentage of renewable carbon in a material (solid or liquid) can be measured with an accelerator mass spectrometer.[88][89]
There is an important difference between biodegradability and biobased content. A bioplastic such as high-density polyethylene (HDPE)[90] can be 100% biobased (i.e. contain 100% renewable carbon), yet be non-biodegradable. These bioplastics such as HDPE nonetheless play an important role in greenhouse gas abatement, particularly when they are combusted for energy production. The biobased component of these bioplastics is considered carbon-neutral since their origin is from biomass.
Anaerobic biodegradability – ASTM D5511-02 and ASTM D5526
The ASTM D5511-12 and ASTM D5526-12 are testing methods that comply with international standards such as the ISO DIS 15985 for the biodegradability of plastic.
See also
- Alkane
- Angewandte Chemie
- Biofuel
- Biopolymer
- BioSphere Plastic
- Organisms breaking down plastic
- Celluloid
- Edible tableware
- Food vs. fuel
- Galalith
- Organic photovoltaics
References
- Andreas Künkel, Johannes Becker, Lars Börger, Jens Hamprecht, Sebastian Koltzenburg, Robert Loos, Michael Bernhard Schick, Katharina Schlegel, Carsten Sinkel, Gabriel Skupin and Motonori Yamamoto (2016). Ullmann's Encyclopedia of Industrial Chemistry. Weinheim: Wiley-VCH. pp. 1–29. doi:10.1002/14356007.n21_n01.pub2.CS1 maint: uses authors parameter (link)
- Siracusa, Valentina; Rocculi, Pietro; Romani, Santina; Rosa, Marco Dalla (2008). "Biodegradable polymers for food packaging: A review". Trends in Food Science & Technology. 19 (12): 634–643. doi:10.1016/j.tifs.2008.07.003.
- Vert, Michel (2012). "Terminology for biorelated polymers and applications (IUPAC Recommendations 2012)" (PDF). Pure and Applied Chemistry. 84 (2): 377–410. doi:10.1351/PAC-REC-10-12-04. S2CID 98107080.
- "Bioplastics (PLA) - World Centric". worldcentric.org.
- Chen, G.; Patel, M. (2012). "Plastics derived from biological sources: Present and future: P technical and environmental review". Chemical Reviews. 112 (4): 2082–2099. doi:10.1021/cr200162d. PMID 22188473.
- "Consiglio dei Ministri conferma la messa al bando dei sacchetti di plastica non biodegradabili - Ministero dell'Ambiente e della Tutela del Territorio e del Mare". minambiente.it.
- Suszkiw, Jan (December 2005). "Electroactive Bioplastics Flex Their Industrial Muscle". News & Events. USDA Agricultural Research Service. Retrieved 2011-11-28.
- Khwaldia, Khaoula; Elmira Arab-Tehrany; Stephane Desobry (2010). "Biopolymer Coatings on Paper Packaging Materials". Comprehensive Reviews in Food Science and Food Safety. 9 (1): 82–91. doi:10.1111/j.1541-4337.2009.00095.x.
- Bio-based drop-in, smart drop-in and dedicated chemicals
- Duurzame bioplastics op basis van hernieuwbare grondstoffen
- What are bioplastics?
- Drop in bioplastics
- Bio-based drop-in, smart drop-in and dedicated chemicals
- Drop in bioplastics
- "Types of Bioplastic | InnovativeIndustry.net". Retrieved 2020-07-11.
- Make Potato Plastic!. Instructables.com (2007-07-26). Retrieved 2011-08-14.
- Liu, Hongsheng; Xie, Fengwei; Yu, Long; Chen, Ling; Li, Lin (2009-12-01). "Thermal processing of starch-based polymers". Progress in Polymer Science. 34 (12): 1348–1368. doi:10.1016/j.progpolymsci.2009.07.001. ISSN 0079-6700.
- Li, Ming; Liu, Peng; Zou, Wei; Yu, Long; Xie, Fengwei; Pu, Huayin; Liu, Hongshen; Chen, Ling (2011-09-01). "Extrusion processing and characterization of edible starch films with different amylose contents". Journal of Food Engineering. 106 (1): 95–101. doi:10.1016/j.jfoodeng.2011.04.021. ISSN 0260-8774.
- Liu, Hongsheng; Yu, Long; Xie, Fengwei; Chen, Ling (2006-08-15). "Gelatinization of cornstarch with different amylose/amylopectin content". Carbohydrate Polymers. 65 (3): 357–363. doi:10.1016/j.carbpol.2006.01.026. ISSN 0144-8617.
- Xie, Fengwei; Yu, Long; Su, Bing; Liu, Peng; Wang, Jun; Liu, Hongshen; Chen, Ling (2009-05-01). "Rheological properties of starches with different amylose/amylopectin ratios". Journal of Cereal Science. 49 (3): 371–377. doi:10.1016/j.jcs.2009.01.002. ISSN 0733-5210.
- Khalid, Saud; Yu, Long; Meng, Linghan; Liu, Hongsheng; Ali, Amjad; Chen, Ling (2017). "Poly(lactic acid)/starch composites: Effect of microstructure and morphology of starch granules on performance". Journal of Applied Polymer Science. 134 (46): n/a. doi:10.1002/app.45504.
- "Starch based Bioplastic Manufacturers and Suppliers". bioplasticsonline.net. Archived from the original on August 14, 2011.
- Sherman, Lilli Manolis (1 July 2008). "Enhancing biopolymers: additives are needed for toughness, heat resistance & processability". Plastics Technology. Archived from the original on 17 April 2016.
- "BASF announces major bioplastics production expansion". Archived from the original on 2012-03-31. Retrieved 2011-08-31.
- "Roquette, nouvel acteur sur le marché des plastiques, lance GAÏALENE® : une gamme innovante de plastique végétal". Archived from the original on 2012-03-31. Retrieved 2011-08-31.
- Avérous, Luc; Pollet, Eric (2014), "Nanobiocomposites Based on Plasticized Starch", Starch Polymers, Elsevier, pp. 211–239, doi:10.1016/b978-0-444-53730-0.00028-2, ISBN 9780444537300
- Avant, Sandra (April 2017). "Better Paper, Plastics With Starch". USDA. Archived from the original on 2018-12-14. Retrieved 2018-12-14.
- Cate, Peter (January 2017). "Collaboration delivers better results". Reinforced Plastics. 61 (1): 51–54. doi:10.1016/j.repl.2016.09.002. ISSN 0034-3617.
- Xie, Fengwei; Pollet, Eric; Halley, Peter J.; Avérous, Luc (2013-10-01). "Starch-based nano-biocomposites". Progress in Polymer Science. Progress in Bionanocomposites: from green plastics to biomedical applications. 38 (10): 1590–1628. doi:10.1016/j.progpolymsci.2013.05.002. ISSN 0079-6700.
- Song, Na; Hou, Xingshuang; Chen, Li; Cui, Siqi; Shi, Liyi; Ding, Peng (2017-05-16). "A Green Plastic Constructed from Cellulose and Functionalized Graphene with High Thermal Conductivity". ACS Applied Materials & Interfaces. 9 (21): 17914–17922. doi:10.1021/acsami.7b02675. ISSN 1944-8244. PMID 28467836.
- Song, J. H.; Murphy, R. J.; Narayan, R.; Davies, G. B. H. (2009-07-27). "Biodegradable and compostable alternatives to conventional plastics". Philosophical Transactions of the Royal Society B: Biological Sciences. 364 (1526): 2127–2139. doi:10.1098/rstb.2008.0289. ISSN 0962-8436. PMC 2873018. PMID 19528060.
- Ralston, Brian E.; Osswald, Tim A. (February 2008). "The History of Tomorrow's Materials: Protein-Based Biopolymers". Plastics Engineering. 64 (2): 36–40. doi:10.1002/j.1941-9635.2008.tb00292.x. ISSN 0091-9578.
- Zhang, Jinwen; Jiang, Long; Zhu, Linyong; Jane, Jay-lin; Mungara, Perminus (May 2006). "Morphology and Properties of Soy Protein and Polylactide Blends". Biomacromolecules. 7 (5): 1551–1561. doi:10.1021/bm050888p. ISSN 1525-7797. PMID 16677038.
- "History, Travel, Arts, Science, People, Places". smithsonianmag.com.
- "Mirel: PHAs grades for Rigid Sheet and Thermoforming". Archived from the original on 2012-03-31. Retrieved 2011-08-31.
- "Micromidas is using carefully constructed populations of bacteria to convert organic waste into bio-degradable plastics". Archived from the original on October 23, 2011.
- "Home". dsm.com.
- Nohra, Bassam; Laure Candy; Jean-Francois Blanco; Celine Guerin; Yann Raoul; Zephirin Mouloungui (2013). "From Petrochemical Polyurethanes to Biobased Polyhydroxyurethanes" (PDF). Macromolecules. 46 (10): 3771–3792. Bibcode:2013MaMol..46.3771N. doi:10.1021/ma400197c.
- Fortman, David J.; Jacob P. Brutman; Christopher J. Cramer; Marc A. Hillmyer; William R. Dichtel (2015). "Mechanically Activated, Catalyst-Free Polyhydroxyurethane Vitrimers". Journal of the American Chemical Society. 137 (44): 14019–14022. doi:10.1021/jacs.5b08084. PMID 26495769.
- Meier, Michael A. R.; Metzger, Jürgen O.; Schubert, Ulrich S. (2007-10-02). "Plant oil renewable resources as green alternatives in polymer science". Chemical Society Reviews. 36 (11): 1788–802. doi:10.1039/b703294c. ISSN 1460-4744. PMID 18213986.
- Floros, Michael; Hojabri, Leila; Abraham, Eldho; Jose, Jesmy; Thomas, Sabu; Pothan, Laly; Leao, Alcides Lopes; Narine, Suresh (2012). "Enhancement of thermal stability, strength and extensibility of lipid-based polyurethanes with cellulose-based nanofibers". Polymer Degradation and Stability. 97 (10): 1970–1978. doi:10.1016/j.polymdegradstab.2012.02.016.
- Pillai, Prasanth K. S.; Floros, Michael C.; Narine, Suresh S. (2017-07-03). "Elastomers from Renewable Metathesized Palm Oil Polyols". ACS Sustainable Chemistry & Engineering. 5 (7): 5793–5799. doi:10.1021/acssuschemeng.7b00517.
- Can, E.; Küsefoğlu, S.; Wool, R. P. (2001-07-05). "Rigid, thermosetting liquid molding resins from renewable resources. I. Synthesis and polymerization of soy oil monoglyceride maleates". Journal of Applied Polymer Science. 81 (1): 69–77. doi:10.1002/app.1414. ISSN 1097-4628.
- Stemmelen, M.; Pessel, F.; Lapinte, V.; Caillol, S.; Habas, J.-P.; Robin, J.-J. (2011-06-01). "A fully biobased epoxy resin from vegetable oils: From the synthesis of the precursors by thiol-ene reaction to the study of the final material" (PDF). Journal of Polymer Science Part A: Polymer Chemistry. 49 (11): 2434–2444. Bibcode:2011JPoSA..49.2434S. doi:10.1002/pola.24674. ISSN 1099-0518.
- Meier, Michael A. R. (2009-07-21). "Metathesis with Oleochemicals: New Approaches for the Utilization of Plant Oils as Renewable Resources in Polymer Science". Macromolecular Chemistry and Physics. 210 (13–14): 1073–1079. doi:10.1002/macp.200900168. ISSN 1521-3935.
- Mata, Teresa M.; Martins, António A.; Caetano, Nidia. S. (2010). "Microalgae for biodiesel production and other applications: A review". Renewable and Sustainable Energy Reviews. 14 (1): 217–232. doi:10.1016/j.rser.2009.07.020. hdl:10400.22/10059.
- Gironi, F., and Vincenzo Piemonte. “Bioplastics and Petroleum-Based Plastics: Strengths and Weaknesses.” Energy Sources, Part A: Recovery, Utilization and Environmental Effects, vol. 33, no. 21, 2011, pp. 1949–59, doi:10.1080/15567030903436830.
- Yates, Madeleine R., and Claire Y. Barlow. “Life Cycle Assessments of Biodegradable, Commercial Biopolymers - A Critical Review.” Resources, Conservation and Recycling, vol. 78, Elsevier B.V., 2013, pp. 54–66, doi:10.1016/j.resconrec.2013.06.010.
- "Are biodegradable plastics better for the environment?". Axion. 6 February 2018. Retrieved 2018-12-14.
- Miles, Lindsay (22 March 2018). "Biodegradable Plastic: Is It Really Eco-Friendly?". Retrieved 2018-12-14.
- Weiss, Martin, et al. “A Review of the Environmental Impacts of Biobased Materials.” Journal of Industrial Ecology, vol. 16, no. SUPPL.1, 2012, doi:10.1111/j.1530-9290.2012.00468.x.
- Brockhaus, Sebastian, et al. “A Crossroads for Bioplastics: Exploring Product Developers’ Challenges to Move beyond Petroleum-Based Plastics.” Journal of Cleaner Production, vol. 127, Elsevier Ltd, 2016, pp. 84–95, doi:10.1016/j.jclepro.2016.04.003.
- Sinha, E., et al. “Eutrophication Will Increase during the 21st Century as a Result of Precipitation Changes.” Science, vol. 357, no. July, 2017, pp. 405–08.
- Rosas, Francisco, et al. “Nitrous Oxide Emission Reductions from Cutting Excessive Nitrogen Fertilizer Applications.” Climatic Change, vol. 132, no. 2, 2015, pp. 353–67, doi:10.1007/s10584-015-1426-y.
- Gironi, F., and Vincenzo Piemonte. “Land-Use Change Emissions: How Green Are the Bioplastics?” Environmental Progress & Sustainable Energy, vol. 30, no. 4, 2010, pp. 685–691, doi:10.1002/ep.10518.
- The truth of about bioplastics
- Bioplastic Feedstock 1st, 2nd and 3rd Generations
- Degli-Innocenti, Francesco. “Biodegradation of Plastics and Ecotoxicity Testing: When Should It Be Done.” Frontiers in Microbiology, vol. 5, no. SEP, 2014, pp. 1–3, doi:10.3389/fmicb.2014.00475.
- Gómez, Eddie F., and Frederick C. Michel. “Biodegradability of Conventional and Bio-Based Plastics and Natural Fiber Composites during Composting, Anaerobic Digestion and Long-Term Soil Incubation.” Polymer Degradation and Stability, vol. 98, no. 12, 2013, pp. 2583–2591., doi:10.1016/j.polymdegradstab.2013.09.018.
- Emadian, S. Mehdi, et al. “Biodegradation of Bioplastics in Natural Environments.” Waste Management, vol. 59, Elsevier Ltd, 2017, pp. 526–36, doi:10.1016/j.wasman.2016.10.006.
- Barrett, Axel (5 September 2018). "The History and Most Important Innovations of Bioplastics". Bioplastics News.
- "Ready to Grow: The Biodegradable Polymers Market". Plastics Engineering. 72 (3): 1–4. March 2016. doi:10.1002/j.1941-9635.2016.tb01489.x. ISSN 0091-9578.
- Darby, Debra (August 2012). "Bioplastics Industry Report". BioCycle. 53 (8): 40–44.
- Rujnić-Sokele, Maja; Pilipović, Ana (September 2017). "Challenges and Opportunities of Biodegradable Plastics: A Mini Review". Waste Management & Research. 35 (2): 132–140. doi:10.1177/0734242x16683272. PMID 28064843. S2CID 23782848.
- Dolfen, Julia. “Bioplastics- Opportunities and Challenges.” US Composting Council. 2012 Compostable Plastics Symposium, Jan. 2012, Austin, Texas, https://compostingcouncil.org/admin/wp-content/uploads/2012/01/Dolfen.pdf Archived 2018-09-26 at the Wayback Machine
- White, J. L. (December 1998). "Fourth in a Series: Pioneers of Polymer Processing Alexander Parkes". International Polymer Processing. 13 (4): 326. doi:10.3139/217.980326. ISSN 0930-777X. S2CID 137545344.
- Raschka, Achim; Carus, Michael; Piotrowski, Stephan (2013-10-04), "Renewable Raw Materials and Feedstock for Bioplastics", Bio-Based Plastics, John Wiley & Sons Ltd, pp. 331–345, doi:10.1002/9781118676646.ch13, ISBN 9781118676646
- "Soybean Car - The Henry Ford". www.thehenryford.org. Retrieved 2020-12-09.
- "A Brief History of Plastic". The Brooklyn Rail. Retrieved 2018-09-27.
- d-2016-154. 2016. doi:10.18411/d-2016-154. ISBN 9785912430725.
- "New fibre could make stronger parts". Reinforced Plastics. 39 (5): 17. May 1995. doi:10.1016/0034-3617(95)91746-2. ISSN 0034-3617.
- "Novamont". Bioplastics News. 2013-12-30. Retrieved 2018-09-27.
- Poirier, Yves; Dennis, Douglas; Klomparens, Karen; Nawrath, Christiane; Somerville, Chris (December 1992). "Perspectives on the production of polyhydroxyalkanoates in plants". FEMS Microbiology Letters. 103 (2–4): 237–246. doi:10.1111/j.1574-6968.1992.tb05843.x. ISSN 0378-1097.
- Lörcks, Jürgen (January 1998). "Properties and applications of compostable starch-based plastic material". Polymer Degradation and Stability. 59 (1–3): 245–249. doi:10.1016/s0141-3910(97)00168-7. ISSN 0141-3910.
- "Monsanto finds buyer for oil and gas assets". Chemical & Engineering News. 63 (48): 5. 1985-12-02. doi:10.1021/cen-v063n048.p005a. ISSN 0009-2347.
- "The History and Most Important Innovations of Bioplastics". Bioplastics News. 2018-07-05. Retrieved 2018-09-27.
- Pennisi, Elizabeth (1992-05-16). "Natureworks". Science News. 141 (20): 328–331. doi:10.2307/3976489. ISSN 0036-8423. JSTOR 3976489.
- DiGregorio, Barry E. (January 2009). "Biobased Performance Bioplastic: Mirel". Chemistry & Biology. 16 (1): 1–2. doi:10.1016/j.chembiol.2009.01.001. ISSN 1074-5521. PMID 19171300.
- Rajam, Manchikatla V.; Yogindran, Sneha (2018), "Engineering Insect Resistance in Tomato by Transgenic Approaches", Sustainable Management of Arthropod Pests of Tomato, Elsevier, pp. 237–252, doi:10.1016/b978-0-12-802441-6.00010-3, ISBN 9780128024416
- "Nanotube technology gains US patent". Reinforced Plastics. 48 (10): 17. November 2004. doi:10.1016/s0034-3617(04)00461-8. ISSN 0034-3617.
- Bayer, Ilker S.; Guzman-Puyol, Susana; Heredia-Guerrero, José Alejandro; Ceseracciu, Luca; Pignatelli, Francesca; Ruffilli, Roberta; Cingolani, Roberto; Athanassiou, Athanassia (2014-07-15). "Direct Transformation of Edible Vegetable Waste into Bioplastics". Macromolecules. 47 (15): 5135–5143. Bibcode:2014MaMol..47.5135B. doi:10.1021/ma5008557. ISSN 0024-9297.
- Sharif Hossain, A.B.M.; Ibrahim, Nasir A.; AlEissa, Mohammed Saad (September 2016). "Nano-cellulose derived bioplastic biomaterial data for vehicle bio-bumper from banana peel waste biomass". Data in Brief. 8: 286–294. doi:10.1016/j.dib.2016.05.029. ISSN 2352-3409. PMC 4906129. PMID 27331103.
- Brodin, Malin; Vallejos, María; Opedal, Mihaela Tanase; Area, María Cristina; Chinga-Carrasco, Gary (September 2017). "Lignocellulosics as sustainable resources for production of bioplastics – A review". Journal of Cleaner Production. 162: 646–664. doi:10.1016/j.jclepro.2017.05.209. ISSN 0959-6526.
- Benvenuto, Mark A. (2018-01-20). "26 Biofuels and bioplastics". doi:10.1515/spark.32.27. Cite journal requires
|journal=
(help) - Tran, Thang Hong, Nguyen, Hoang-Linh, Hwang, Dong Soo, Lee, Ju Young, Cha, Hyun Gil, Koo, Jun Mo, Hwang, Sung Yeon, Park, Jeyoung, Oh, Dongyeop X. (2019). "Five different chitin nanomaterials from identical source with different advantageous functions and performances". Carbohydrate Polymers. Elsevier Science B.V., Amsterdam. 205 (– [2019]): 392–400. doi:10.1016/j.carbpol.2018.10.089. ISSN 0144-8617. PMID 30446120.CS1 maint: multiple names: authors list (link)
- "Compostable.info".
- "ASTM D6002 - 96(2002)e1 Standard Guide for Assessing the Compostability of Environmentally Degradable Plastics (Withdrawn 2011)". astm.org.
- "ASTM D6866 - 11 Standard Test Methods for Determining the Biobased Content of Solid, Liquid, and Gaseous Samples Using Radiocarbon Analysis". Astm.org. Retrieved 2011-08-14.
- "NNFCC Newsletter – Issue 16. Understanding Bio-based Content — NNFCC". Nnfcc.co.uk. 2010-02-24. Retrieved 2011-08-14.
- "Braskem". Braskem. Retrieved 2011-08-14.
Further reading
- Plastics Without Petroleum History and Politics of 'Green' Plastics in the United States
- Plastics and the environment
- "The Social construction of Bakelite: Toward a theory of invention" in The Social Construction of Technological Systems, pp. 155–182
External links
![]() |
Wikimedia Commons has media related to Bioplastics. |
- Bioplastics at Agriculture and Agrifood Canada
- Plastics 2020 Challenge: Debate on the future role of Bioplastics
- Assessment of China's Market for Biodegradable Plastics, May 2017, GCiS China Strategic Research