CFM International LEAP
The CFM International LEAP ("Leading Edge Aviation Propulsion"[8]) is a high-bypass turbofan produced by CFM International, a 50-50 joint venture between American GE Aviation and French Safran Aircraft Engines (formerly Snecma), the successor of the successful CFM56 competing with the Pratt & Whitney PW1000G to power narrow-body aircraft.
LEAP | |
---|---|
![]() | |
Mockup of a LEAP-X, the early code name of the engine | |
Type | Turbofan |
National origin | France, United States |
Manufacturer | CFM International |
First run | 4 September 2013 (LEAP-1A)[1] 13 June 2014 (LEAP-1B)[2] 9 October 2014 (LEAP-1C)[3] |
Major applications | Airbus A320neo family Boeing 737 MAX Comac C919 |
Number built | 2516+[lower-alpha 1] |
Developed from | CFM International CFM56 General Electric GEnx |
Developed into | General Electric Passport |
Design
The LEAP's basic architecture includes a scaled-down version of Safran's low pressure turbine used on the GEnx engine. The fan has flexible blades manufactured by a resin transfer molding process, which are designed to untwist as the fan's rotational speed increases. While the LEAP is designed to operate at a higher pressure than the CFM56 (which is partly why it is more efficient), GE plans to set the operating pressure lower than the maximum to maximize the engine's service life and reliability.[9] Currently proposed for the LEAP is a greater use of composite materials, a blisk fan in the compressor, a second-generation Twin Annular Pre-mixing Swirler (TAPS II) combustor, and a bypass ratio around 10-11:1.
GE is using ceramic matrix composites (CMC) to build the turbine shrouds.[10] These technological advances are projected to produce 16% lower fuel consumption.[11][12] Reliability is also supported by use of an eductor-based oil cooling system similar to that of the GEnx, featuring coolers mounted on the inner lining of the fan duct. According to Aviation Week's article, "The eductor device produces a venturi effect, which ensures a positive pressure to keep oil in the lower internal sump."[9] The engine has some of the first FAA-approved 3D-printed components.[13]
Development
The LEAP ("Leading Edge Aviation Propulsion")[15] incorporates technologies that CFM developed as part of the LEAP56 technology acquisition program, which CFM launched in 2005.[16] The engine was officially launched as LEAP-X on 13 July 2008.[11] It is intended to be a successor to the CFM56-5B and CFM56-7B.
In 2009, COMAC selected the LEAP engine for the C919.[17] The aircraft was due to begin testing in 2016.[18] In total, 28 test engines will be used by CFM to achieve engine certification, and 32 others will be used by Airbus, Boeing and COMAC for aircraft certification and test programs.[1][19] The first engine entering the test program reached and sustained 33,000 lbf (150 kN) of thrust, required to satisfy the highest rating for the Airbus A321neo. The same engine ultimately reached 35,000 lbf (160 kN) of thrust in test runs.[9]
General Electric carried out the first test flight, of a LEAP-1C, in Victorville, California, with the engine mounted on the company's Boeing 747 flying testbed aircraft, on October 6, 2014. The -1C version features a thrust reverser equipped with a one piece O-ring replacing a 2 piece door. The thrust reverser is deployed by the O-ring sliding aft, reducing the drag that was induced by the older design and improving efficiency.[20] In April 2015, it was reported that the LEAP-1B was suffering up to a 5% shortfall on its promised reduction in fuel consumption.[21] It obtained its 180-minute ETOPS approval from the U.S. Federal Aviation Authority and the European Aviation Safety Agency on June 19, 2017.[22]
Orders
On July 20, 2011, American Airlines announced that it planned to purchase 100 Boeing 737 aircraft featuring the LEAP-1B engine.[23] The project was approved by Boeing on August 30, 2011 as the Boeing 737 MAX.[24][25] Southwest Airlines is the launch customer of the 737 MAX with a firm order of 150 aircraft.[26]
CFM International offers its support for the engine, and signed a 15-year Rate per Flight Hour agreement with Loong Air for 20 LEAP-1A at U.S $333 million, or $3039 per engine per day, in contrast with U.S. $138 million for 17 CFM International CFM56 over 12 years or $1852 per engine per day.[27] As a number of A320neo engine for ANA group of Japan was also ordered in 2014, there is a possibility to select the LEAP engine.[28]
In 2016 CFM booked 1,801 orders, LEAP backlog is at more than 12,200 for more than $170 billion U.S. at list price.[4] In early 2018, the backlog was at 14,500, with a 59% share of the A320neo market for decided customers as it has an 18 percentage point advantage in utilization rate over the Pratt & Whitney PW1000G.[29]
By July 2018, the LEAP had an eight-year backlog with 16,300 sales. More LEAPs were produced in the five years to 2018 than CFM56s in 25 years.[5] It is the second-most ordered jet engine behind the 44-year-old CFM56,[30] which achieved 35,500 orders.[5] In July 2018 its A320neo selected-engine market share was 58.6%, with one-third yet to select, the CFM56 have a 60% share of the A320ceo market.[30]
Production
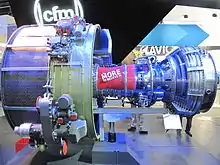
In 2016, the engine was introduced in August on the Airbus A320neo with Pegasus Airlines and CFM delivered 77 LEAP.[4] With the 737 MAX introduction, CFM delivered 257 LEAPs in the first three quarters of 2017, including 110 in the third: 49 to Airbus and 61 to Boeing, and targets 450 in the year.[31] CFM was to produce 1,200 engines in 2018, 1,900 in 2019, and 2,100 in 2020.[32] This is compared to the 1,700 CFM56 produced in 2016.[33]
To cope with the demand, CFM is duplicating supply sources on 80% of parts and even subdivide assembly sites, already shared between GE and Safran. GE assembles its production in Lafayette, Indiana, US in addition to its previous Durham, North Carolina, US facility. As more than 75% of the engine comes from suppliers, critical parts suppliers pass “run-rate stress tests” lasting two to 12 weeks. Pratt & Whitney acknowledges a production ramp-up bottleneck on its rival PW1100G geared turbofan including a critical shortage of the unique aluminium-titanium fan blade, hitting the Airbus A320neo and the Bombardier CSeries deliveries.[34] Safran assembles its production in Villaroche, France, Safran and GE each assemble half of the annual volume.[35] Mecachrome plan to produce 120,000-130,000 LEAP turbine blades in 2018 up from 50,000 in 2017.[36]
In mid-June 2018, deliveries remained four to five weeks behind schedule down from six, and should catch up in the fourth quarter as the quality variation of castings and forgings improves. The production has no single manufacturing choke point by selecting multiple suppliers for every critical part. From 460 in 2017, 1,100 LEAPs should be built in 2018, along 1,050 CFM56s as it encounter unexpected sales, to pass the record production of 1,900 engines in 2017. It will stay over 2,000 engines per year as 1,800 LEAPs should be produced in 2019 while CFM56 production will drop, then 2,000 in 2020.[5] In 2018, 1,118 engines were delivered.[6]
Over the first half of 2019, CFM revenues were up by 23% to €5.9 billion with 1,119 deliveries included a declining 258 CFM56s, more than offsetted by 861 LEAPs. Recurring operating income rose by 34% to €1.2 billion, but was reduced by €107 million ($118 million) due to the negative margins and initial costs of LEAP production, before a positive contribution expected in the second half. Revenues should grow by 15% in 2019 but free cash flow depends on the return to service of the grounded 737 MAX.[7]
In 2019, Leap production rose to 1,736 engines, orders and commitments reached 1,968 amid the 737 MAX groundings, compared with 3,211 for 2018, for a stable backlog of 15,614 (compared to 15,620). CFM expects to produce 1,400 Leap engines in 2020, including an average of 10 weekly Leap-1Bs for the Boeing 737 Max.[37]
Operations
The troubled introduction of the PW1100G on the A320neo has motivated customers to choose LEAP engines. LEAP market share rose from 55% to 60% in 2016, but orders for 1,523 aircraft (29%) had not specified which engine would be chosen.[38] From January through early August 2017, 39 PW1100G engines versus 396 CFM LEAP engines were chosen. As an example of PW1100G reliability issues, 9% of LEAP-powered A320neos were out of service for at least one week in July 2017, compared with 46% of those using the PW1100G.[38]
The Boeing 737 MAX LEAP-1B started revenue service in May 2017 with Malindo Air with 8 hours of daily operation, while the A320neo LEAP-1A surpassed 10 hours per day by July. Safran discovered a production quality defect on LEAP-1B low-pressure turbine disks during assembly for possibly 30 engines and CFM is working to minimize flight-test and customer-delivery disruptions.[39]
In early October 2017, an exhaust gas temperature shift was noticed during a flight and a CMC shroud coating in the HP turbine was seen flaking off in a borescope inspection, creating a leaking gap: eight in-service engines are seeing their coating replaced.[40] Safran provisioned €50 million ($58 million) to trouble-shoot in-service engines, including potentially LEAP-1Bs.[31] Forty LEAP-1A were replaced and the part should be replaced in over 500 in-service engines, while shipments are four weeks behind schedule.[41] Deliveries with the permanent CMC environmental-barrier coating fix began in June.[42]
On March 26, 2019, during the Boeing 737 MAX groundings, Southwest Airlines flight 8701 (737 MAX 8) took off from Orlando International Airport for a ferry flight without passengers, but soon after problems with one of the engines caused an emergency landing at the same airport. Southwest then inspected 12 LEAP engines and two other airlines also inspected their engines.[43] CFM recommended replacing the fuel nozzles more often due to coking, a carbon buildup.[44]
Applications
Model | Application | Thrust range | Introduction |
---|---|---|---|
-1A | Airbus A320neo family | 24,500–35,000 lbf (109–156 kN) | 2 Aug 2016[46] |
-1B | Boeing 737 MAX | 23,000–28,000 lbf (100–120 kN) | 22 May 2017[47] |
-1C | COMAC C919 | 27,980–30,000 lbf (124.5–133.4 kN) | 2021[48] |
- The LEAP-1A installed on the Airbus A320neo family.
- The LEAP-1B installed on the Boeing 737 MAX.
- The LEAP-1C is the exclusive engine option for the Chinese Comac C919.
Specifications
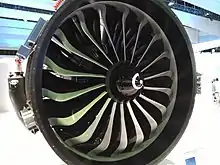
Model | LEAP-1A[49] | LEAP-1B[50] | LEAP-1C[49] |
---|---|---|---|
Configuration | Twin-spool, high bypass turbofan | ||
Compressor | 1 fan, 3-stage LP, 10-stage HP[51] | ||
Combustor | Second generation Twin-Annular, Pre-Mixing Swirler Combustor (TAPS II)[45] | ||
Turbine | 2-stage HP, 7-stage (-1B: 5-stage) LP[52] | ||
OPR | 40:1[51] (50:1, Top-of-Climb) | ||
TSFC | ~ -15% (vs. current CFM56 engine)[45] (~0.53–0.56 lb/lbf/h (15–16 g/kN/s)[53]) | 0.51 lb/lbf/h (14 g/kN/s)[54] | |
Fan diameter[51] | 78 in (198 cm) | 69.4 in (176 cm) | 77 in (196 cm)[55] |
Bypass ratio[51] | 11:1 | 9:1 | 11:1 |
Length | 3.328 m (131.0 in) [lower-alpha 2] | 3.147 m (123.9 in) | 4.505 m (177.4 in) [lower-alpha 3] |
Max. Width | 2.533–2.543 m (99.7–100.1 in) | 2.421 m (95.3 in) | 2.659 m (104.7 in) |
Max. Height | 2.368–2.362 m (93.2–93.0 in) | 2.256 m (88.8 in) | 2.714 m (106.9 in) |
Weight | 2,990–3,153 kg (6,592–6,951 lb) (Wet) | 2,780 kg (6,130 lb) (Dry) | 3,929–3,935 kg (8,662–8,675 lb) (Wet) |
Max. Take-Off thrust | 143.05 kN (32,160 lbf) | 130.41 kN (29,320 lbf) | 137.14 kN (30,830 lbf) |
Max. Continuous | 140.96 kN (31,690 lbf) | 127.62 kN (28,690 lbf) | 133.22 kN (29,950 lbf) |
Max. rpm | LP : 3894, HP : 19391 | LP : 4586, HP : 20171 | LP : 3894, HP : 19391 |
Variant | Take-Off Thrust | Max. Continuous |
---|---|---|
-1A23 | 106.80 kN (24,010 lbf) | 104.58 kN (23,510 lbf) |
-1A24 | 106.80 kN (24,010 lbf) | 106.76 kN (24,000 lbf) |
-1B25 | 119.15 kN (26,790 lbf) | 115.47 kN (25,960 lbf) |
-1A26 | 120.64 kN (27,120 lbf) | 118.68 kN (26,680 lbf) |
-1B27 | 124.71 kN (28,040 lbf) | 121.31 kN (27,270 lbf) |
-1B28 | 130.41 kN (29,320 lbf) | 127.62 kN (28,690 lbf) |
-1C28 | 129.98 kN (29,220 lbf) | 127.93 kN (28,760 lbf) |
-1C30 | 137.14 kN (30,830 lbf) | 133.22 kN (29,950 lbf) |
-1A30, 32, 33, 35A | 143.05 kN (32,160 lbf) | 140.96 kN (31,690 lbf) |
See also
Related development
Comparable engines
Related lists
References
- "CFM launches a new era as first LEAP engine begins ground testing". CFM International. 2013-09-06. Retrieved 2013-09-07.
- "CFM International démarre le premier LEAP-1B du 737 MAX". Le journal de l'aviation. 2014-06-18. Retrieved 2015-03-05.
- "Leap 1C Engine Tests Continue as Comac's C919 Takes Shape". AIN-Online. 2014-11-10. Retrieved 2016-03-15.
- "2016 CFM orders surpass 2,600 engines" (Press release). CFM International. 14 February 2017.
- Chris Kjelgaard (July 4, 2018). "CFM Confident Leap Production Can Catch Up Soon". AIN online.
- Jon Hemmerdinger (1 Feb 2019). "MID SUPPLY CHAIN RECOVERY CFM's Leap deliveries doubled in 2018 amid supply chain recovery". Flightglobal.
- David Kaminski-Morrow (5 Sep 2019). "Leap production edges towards positive contribution". Flightglobal.
- "Aircraft engines". Safran.
- Guy Norris (Oct 28, 2013). "Smooth Start To Fast-Paced Leap-1A Test Program". "Pressure testing". Aviation Week & Space Technology. p. 43.
- Guy Norris (Apr 13, 2015). "Pratt Targets Hot, Rotating Blade Use Of CMCs". "Hot blades" (PDF). Aviation Week & Space Technology. April 27, 2015. p. 55.
- "CFM Unveils New LEAP-X Engine" (Press release). CFM International. 2008-07-13.
- "New engines: flurry of activity despite downturn". Flightglobal. 2009-10-06.
- Tomas Kellner (Apr 14, 2015). "The FAA Cleared the First 3D Printed Part to Fly in a Commercial Jet Engine from GE". GE.
- Guy Norris (Nov 20, 2015). "CFM Lifts Veil On Leap Engine Test Details". Aviation Week & Space Technology.
- LEAP Turbofan Engine, History
- CFM Laying the Technology Foundation for the Future Archived 2011-06-23 at WebCite. CFM International
- "CFM International to provide engines for COMAC's C919". flightglobal. 21 Dec 2009.
- "CFM to finish Leap core testing by mid-May". flightglobal. 28 Apr 2010.
- david kaminski morrow (22 Apr 2015). "First Leap-powered A320neo moved to flight-test team". flightglobal.
- Guy Norris (October 13, 2014). "CFM Marks 40th Anniversary With Leap-1 Flight Test". Aviation Week & Space Technology. p. 40.
- "Engine problems aren't Propulsion South Carolina's problem".
- "LEAP engines awarded 180-minute ETOPS certification" (Press release). CFM International. Jun 21, 2017.
- "Boeing and American Airlines Agree on Order for up to 300 Airplanes - Jul 20, 2011". Boeing.mediaroom.com. July 20, 2011. Retrieved May 31, 2013.
- Boeing Confirms Duopoly With Airbus Announcing Re-Engining Of 737. Forbes
- Boeing rendering illustrates major changes to 737NE. flightglobal.com
- "Southwest Airlines Will Become Launch Customer for the New Boeing 737 Max Aircraft - Southwest Airlines Newsroom". Swamedia.com. December 13, 2011. Archived from the original on 2014-10-15. Retrieved May 31, 2013.
- "Zhejiang Loong Air signs RPFH agreement for CFM56-5B engines". Aviation News Ltd. 15 June 2015.
- "Zhejiang Loong Air signs Service agreement for CFM LEAP-1A engines". Aviation News Ltd. 15 June 2015.
- "GE/CFM in "lockstep" with Boeing on NMA". Leeham News. March 22, 2018.
- Stephen Trimble (15 July 2018). "CFM looks to another Leap forward at Farnborough". Flightglobal.
- Sean Broderick (Oct 31, 2017). "Safran Reveals Leap Turbine Shroud Coating Issue Issue". Aviation Week Network.
- Stephen Trimble (June 19, 2017). "GE ups production target to meet Boeing and Airbus demand". Flight Global.
- Max Kingsley-Jones (November 15, 2016). "CFM quietly confident on Leap production ramp-up". Flight Global.
- "New GE plant highlights CFM ramp-up strategy on Leap". Flight Global. 16 November 2016.
- "CFM confirms initial LEAP-1A and LEAP-1B assembly allocation". MRO Network. 2016-12-15. Retrieved 2017-12-24.
- Thierry Dubois (Mar 15, 2018). "Leap Engine Deliveries To Airbus Still Challenging". Aviation Week & Space Technology.
- David Kaminski-Morrow (27 February 2020). "CFM to build 10 737 Max engines weekly for 2020". Flightglobal.
- Rick Clough (22 Aug 2017). "Pratt's $10 Billion Jet Engine Lags GE by 10-to-1 on New Orders". Bloomberg.
- Sean Broderick (Aug 31, 2017). "Issues With Newest Engines Provide Early MRO-Proving Opportunities". Aviation Week Network.
- Stephen Trimble (30 Oct 2017). "CFM reviews fleet after finding Leap-1A durability issue". Flightglobal.
- Rick Clough and Julie Johnsson (5 March 2018). "Fix for New Boeing, Airbus Planes". Bloomberg.
- Chris Kjelgaard (July 17, 2018). "CFM Fixes Leap Turbine Shroud Coatings". AIN online.
- Schlangenstein, Mary; Clough, Rick; Levin, Alan (April 17, 2019). "Airlines to Conduct Engine Checks on Grounded Boeing Max". Bloomberg News.
- Broderick, Sean (Apr 18, 2019). "CFM Monitoring Leap Fleet For Issue Linked To Southwest Engine Failure". Aviation Week Network.
- "The Leap Engine". CFM International. Retrieved 14 November 2016.
- "Pegasus starts flying Leap-1A-powered A320neo". Flight Global. August 2, 2016. Retrieved August 3, 2016.
- "Malindo operates world's first 737 Max flight". Flight Global. May 22, 2017.
- Brenda Goh (5 February 2018). "China's COMAC says first delivery of C919 jet planned for 2021". Reuters.
- "Type Certificate data sheet for LEAP-1A & LEAP-1C Series Engines" (PDF). EASA. 30 May 2018. Archived from the original (PDF) on 13 October 2018. Retrieved 12 October 2018.
- "Type Certificate data sheet for LEAP-1B Series Engines" (PDF). EASA. 16 June 2017. Archived from the original (PDF) on 4 April 2018. Retrieved 4 April 2018.
- "LEAP overview" (PDF). CFM International. June 2017.
- "Comparing the new technology Narrow-body engines: GTF vs LEAP maintenance costs". Airinsight. November 9, 2011. Retrieved May 31, 2013.
- Bjorn Fehrm (19 Jan 2015). "Fundamentals of airliner performance, Part 6; The engine". Leeham News.
- Fomin, Andrey (December 2011). "PD-14: New generation engine for MC-21". Take-off. pp. 20–21.
- "LEAP-1C: integrated propulsion system for the Comac C919". Safran Aircraft Engines. June 2015.
External links
![]() |
Wikimedia Commons has media related to CFM International LEAP. |
- CFM LEAP page
- CFM Unveils New LEAP-X Engine
- CFM ready to advance LEAP-X schedule; opens way for 737RE
- A320 re-engine decision in 2010
- Plane makers switch to cleaner engines