Blowoff valve
A blow-off valve (BOV), dump valve or compressor bypass valve (CBV), is a pressure release system present in most turbocharged engines. Its main purpose is to take the load off the turbocharger when the throttle is suddenly closed.[1]
Characteristics

A compressor bypass valve (CBV), also known as a pressure relief valve or diverter valve, is a manifold vacuum-actuated valve designed to release pressure in the intake system of a turbocharged vehicle when the throttle is lifted or closed. This air pressure is re-circulated back into the non-pressurized end of the intake (before the turbo) but after the mass airflow sensor.
A blowoff valve, (sometimes "hooter valve" or BOV) performs the same task but releases the air into the atmosphere instead of recirculating it. This type of valve is typically an aftermarket modification. The blowoff action produces a range of distinctive hissing sounds, depending on the exit design. Some blowoff valves are sold with a trumpet-shaped exit that intentionally amplifies the sound. Some turbocharged vehicle owners may purchase a blowoff valve solely for the auditory effect even when the function is not required by normal engine operation. Motorsports governed by the FIA have made it illegal to vent unmuffled blowoff valves to the atmosphere.
Blowoff valves are used to prevent compressor surge, a phenomenon that readily occurs when lifting off the throttle of an unvented, turbocharged engine. The sound produced is called turbo flutter (the slang term "choo-choo" is sometimes used). When the throttle plate on a turbocharged engine closes, with the turbine spinning at high speed, the flow reduces beyond the surge line of the compressor. At this point the change in pressure across the compressor reduces, leading to a collapse in flow and possibly even flow reversal and a collapse in plenum pressure.[2] As the compressor is still spinning at high speed, once the flow has reduced sufficiently, the change in across the compressor begins to rise and flow is re-established into the plenum. This continues until once again the plenum is pressurised and flow begins to fall until the surge line is again crossed and the cycle repeats.[1][3] This unstable flow leads to the cyclic noise sometimes heard on high boost engines with no bypass valve. With a valve fitted, flow is maintained preventing the compressor entering the stall/surge cycle.
The repeated, high speed cycling will cause a cyclic torque on the compressor and may lead to increased stresses on the bearings and compressor impeller.[2]
Operation

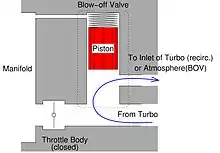
A blowoff valve is connected by a vacuum hose to the intake manifold after the throttle plate. When the throttle is closed, the relative manifold pressure drops below atmospheric pressure and the resulting pressure differential operates the blowoff valve's piston. The excess pressure from the turbocharger is then vented into the atmosphere or recirculated into the intake upstream of the compressor inlet.
Disadvantages
In the case where a mass airflow sensor (MAF) is used and is located upstream from the blowoff valve, the engine control unit (ECU) will inject excess fuel because the atmospherically vented air is not subtracted from the intake charge measurements. The engine then briefly operates with a fuel-rich mixture after each valve actuation.
The rich mixing can lead to hesitation or even stalling of the engine when the throttle is closed, a situation that worsens with higher boost pressures. Occasional events of this type may be only a nuisance, but frequent events can eventually foul the spark plugs and destroy the catalytic converter, as the inefficiently combusted fuel produces soot (excess carbon) and unburned fuel in the exhaust flow can produce soot in the converter and drive the converter beyond its normal operating temperature range.
An alternative method for utilizing both a MAF and a blowoff valve is to have the MAF located down stream between the intercooler and the throttle plate. This is known as Blow-through rather than the traditional Draw-through set up. Care must be taken as to the position of the MAF to prevent damage to the sensitive element. For example, on a SR20DET engine, the MAF must be at least 12 inches (300 mm) from the throttle plate, and the blowoff valve must be 6 inches (150 mm) from the MAF sensor. By using a blow-through method, the MAF won't be affected by the blowoff valve opening as the pressure is vented before the air reaches the MAF.
One approach used to mitigate the problem has been to reduce the boost pressure, which reduces the required venting volume and yields less charge over-calculation by the ECU. The air can also be recirculated back into the intake, a typical stock setup for cars with an upstream MAF sensor. The situation can also be corrected by switching the fuel metering system over to a manifold absolute pressure sensor, a conversion that usually requires a compatible aftermarket ECU or piggy-back fuel controller. The MAP sensor monitors the absolute pressure in the manifold at all times and will correctly detect the change that occurs when the valve vents, allowing the ECU to reduce fuel metering accordingly.
See also
References
- "All you ever needed to know about blow-off valves". www.gfb.com.au. Retrieved 1 September 2018.
- "What is compressor surge?". www.turbobygarrett.com. Retrieved 1 September 2018.
- Xue, Xiang; Wang, Tong; Zhang, Tongtong; Yang, Bo (2018). "Mechanism of stall and surge in a centrifugal compressor with a variable vaned diffuser". Chinese Journal of Aeronautics. 31 (6): 1222–1231. doi:10.1016/j.cja.2018.04.003.
- Allard, Alan. Turbocharging and Supercharging. Cambridge, England: Patrick Stevens Limited, 1982.
- Gorla, Rama, and Khan, Aijaz. Turbomachinery Design and Theory. New York, New York: Marcel Dekker, 2003.
- Society of Automotive Engineers. Turbochargers and Turbocharged Engines. Warrendale, PA, 1979.
- Watson, N, and Janota, N. Turbocharging the Internal Combustion Engine. London, England: Macmillan Press Ltd, 1982.